Three Major Developments in Medical Packaging
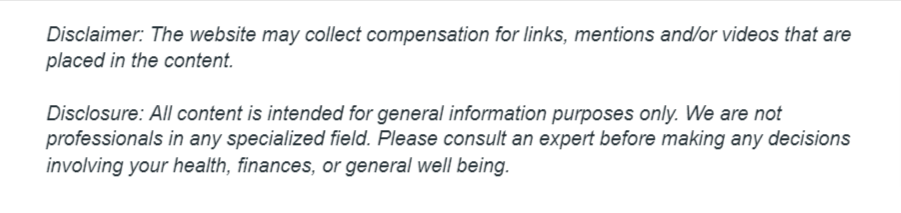

There are a lot of reasons that medical packaging design is a quickly growing industry. Medical packaging techniques are a big part of keeping dangerous medication out of the hands of children who shouldn’t have it, yet also accessible to senior citizens. It is pharma packaging that protects the quality of the medication, to ensure that it both is safe and serves its intended purpose all the way until its expiration date. It is the job of medical packaging to ensure that the drugs that hit the market haven’t been tampered with at any point in the supply chain process.
Some of the technology in medical packaging development is nothing short of space age. Take a look for yourself:
Three Major Developments in Medical Packaging
- Vial Pharmaceutical Packaging
At some pharmacies leave vial pharmaceutical packaging to the pharmacist who manages the pharmacy. This is also the case for many hospitals, relying on the nurses who administer the drugs to provide the vial pharmaceutical packaging and measure the accurate dosage of the medication. There are a few reasons this isn’t ideal. First of all, anything that is managed by a human leaves room for human error. A mistake in the administer of medication could be a deadly mistake. Second of all, when a medication is in a bottle that is open and closed as dosages are removed, it allows air to get to it, which shortens the shelf life of it and heightens the risk of contamination. And finally, for controlled medications, there is less accountability if a dosage can be removed from a bottle without being noticed.
Instead, many pharmaceutical packaging companies are turning to pre-filled single-use vials for their vial pharmaceutical packaging. This removes the opportunity for error since the dosages are automatically filled in advance. It improves the shelf life, as the package is sealed and air tight until it is used. It is a critical step in the medical serialization process, where every step of the pharma supply chain requires accountability, which reduces pharma fraud. It’s a fairly simple change in the way medical vials are processed, but it has far reaching benefits. - Counterfeit-preventing Packaging
It’s no surprise that counterfeit pharmaceuticals are a huge problem in the medical industry. More than $231 billion in medication is sold every year. That’s a lot of money that pumps through the economy. If a person can get a fake medication in the mix, they can take home a sizable amount of cash for it. This is incredibly dangerous for the patients who are taking the medication without knowing that they are counterfeit. Other counterfeiting strategies involve swapping out controlled medications that can be sold for a lot more on the black market with drugs that look identical. This is also extremely dangerous for the public.
Packaging is a huge step in the pharma serialization. Pharma packaging companies employ many of the same tactics that the government uses to prevent counterfeit money. They might add holographic foils to the packaging, so that the fake drugs are immediately distinguishable. They might add tracers to the ink when the packaging is produced; this is virtually impossible to fake. They might include labels with security feature on the packaging. For medication that are particularly costly or prone to counterfeit, some pharma packaging companies actually seal the packaging with diamond dust, as every diamond has a unique fingerprint, leaving it impossible to impersonate. - Self-administer Medication Packaging
Sometimes, when a medication is complicated to administer, it can be particularly difficult for an elderly patient or a patient who needs the medication because they’re disabled to administer it. For example, medications that are injections require the dexterity to push the syringe into the skin with two knuckles and then push the medication in with the thumb. If a patient has to administer their own injection but isn’t capable of this level of dexterity, they might benefit from a medication that administers itself. Some pharma packaging manufacturers create injectables that are spring-loaded to administer themselves when they are pressed against the skin. No dexterity is required.
We want to hear from you. Are you aware of any updates to the pharma packaging industry that make drugs higher-quality and safer to the public? Please share in the comment section below!